"Demingification" of Saga
If Japan Can, Why Can't We?
Around 20 years ago, during my college days I used to drink beer and discuss with fellow students. Through those discussions, we would gather new knowledge in different spheres of life, from history of art and architecture to politics and economics. Friend of ours told us once about the lesson he studied at the University – industrial development of Japan in second half of the 20th century. Without going too much into details he put emphasis on the fact that country which was completely ruined after II WW managed to bounce back and only two decades after two atomic bombs hit its ground became one of the leading economies in the world.
We had drunk a lot more beer together and different topics were discussed, but back then I didn’t manage to understand how Japan reached the current level of economic production and why Japanese companies have such a respectable reputation today.
Several years after that conversation, my girlfriend back then and present wife, was assigned task to research Deming’s methodologies for quality control and to put it in the form of essay.
Me: Who is mister Deming?
Her: Some American guy, who used to work as a consultant in Japanese companies.
I took the paper and longer I had been reading it, something popped into my mind again and again – story about Japan and everything starts to fall into place.
William Edwards Deming
William Edwards Deming
Although poor in natural resources, Japan is nowadays recognized as industrial and economical giant, with extremely high productivity, unexcelled quality of products and very high Human Development Index. However, getting into reading material (with primary task to correct spelling) I found out it wasn’t always that way. In 1950s their products were synonym for bad quality with the lowest price on the market, even called pejoratively “japonesia”
For various geopolitical reasons that were prevalent in the time after II WW (SSSR vs USA), USA wanted to strengthen its influence in the defeated Japan. Various kinds of incentives and help followed, which included hiring experts and consultants with intention to give the benefit of experiences from American companies and to show how is job done there. One of the consultants was Edward Deming, who came with intention to implement Quality Control System in Japanese companies.
Through series of seminars and lectures Deming conveyed his former experience and techniques of improvement and solving problems related to quality. Those techniques included Statistical Quality Control and Statistical Process Control, methodologies that were recognized and efficient in USA.
Deming’s idea was to pass on new business principle and to convince both management in companies and engineers that consumer is main in production chain and that all employees are responsible for final quality of the product. He emphasized that is essential to define needs and desires of consumers. He also pointed out that creation of a quality product demands involvement of teams composed of all company structures – management, marketing, sales, R&D, engineering, design, production, supplies etc.
First lectures took place in 1950 with 400 participants included. At that point he already emphasized that through adoption of adequate standards, proper use of quality control and process control bad reputation of Japanese products could be altered within 5 years. Objective was to create product of high quality and low price which would domineer on the world market.
How wide those courses were recognized and how much attention had been given to them tells us the fact that in next 20 years more than 14000 participants took part in it.
Great number of Japanese manufacturers incorporated Deming’s techniques and in that way elevated their productivity and quality of their products to tremendous heights. Improved quality combined with low costs generated new international demand for Japanese products.
Sony, Toyota, Nissan, Toshiba, Honda, Panasonic, Canon, Fujitsu.
Initial goal of SQC developed in the 30s in USA was to follow production through different stages of procession, to detect and solve problems, and to follow quality of final product/service. Deming improved this method and pointed out that quality comes from process improvement, not from just scanning and analyzing results of bad production.
What often prevails is opinion (wrong opinion) that the one working hard can get anything well done. However, if processes are wrong they cannot produce quality, despite of amount of work invested –Deming.
Over a period of many years working in Japan, Deming modified SPC/SQC processes in the cycle nowadays known as PDSA (Plan-Do-Study-Act).
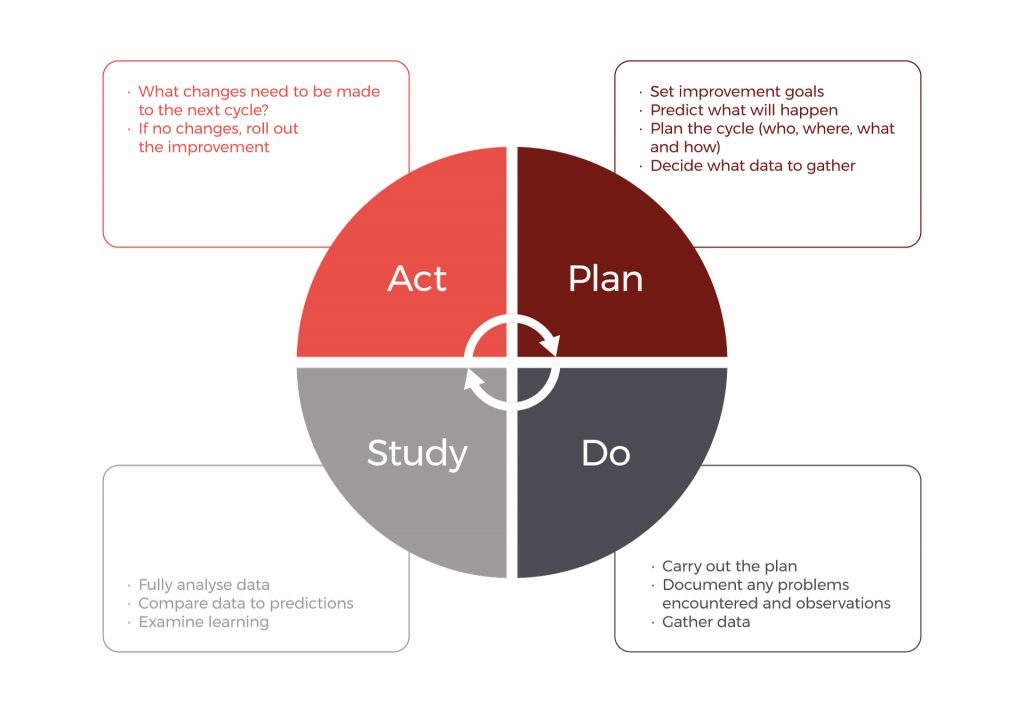
Plan – design and create product thoroughly
Do – make it and test
Study – release it on the market
Act – Do analysis of the market. Discover which status product has in the consumer’s mind and which are the reasons for that.
Plan – Redesign product according to results given in the stage of analysis, PDSA
This is dynamic model which implies that end of one cycle follows beginning of the next one with intention of constant quality improvement where every cycle consist of all the steps. By using what we discovered in one PDSA cycle we can start a new, more complex one.
Realizing potential of PDSA and possibility of its application to every sphere of life (not only production process), Japanese managers transformed PDSA into PDCA methodology.
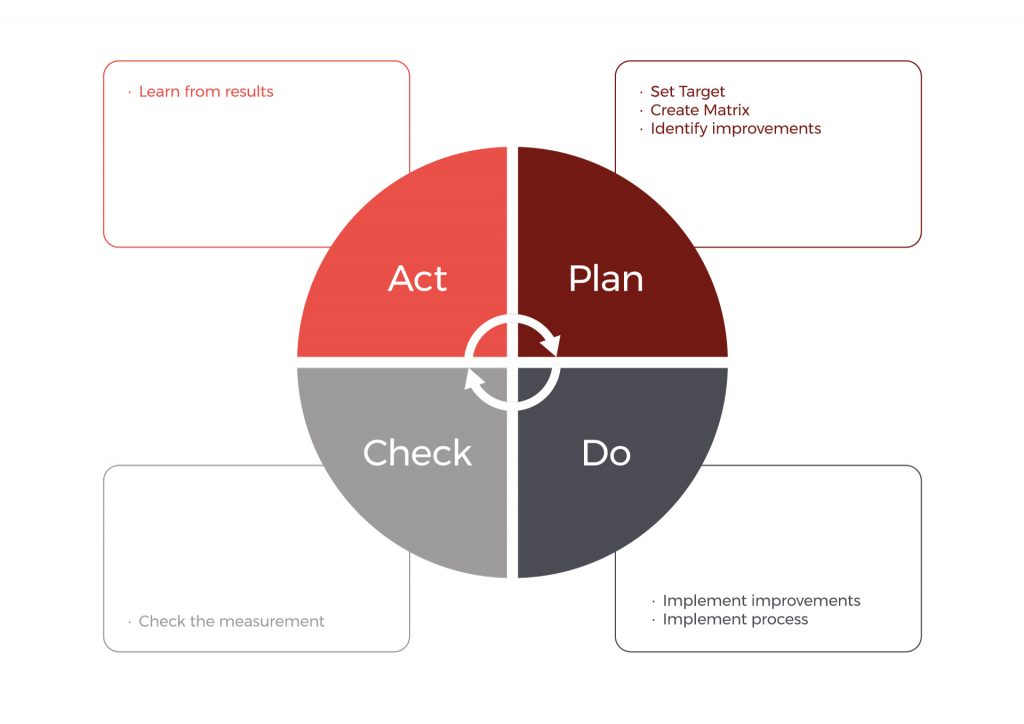
Plan – design and create product thoroughly
Do – make it and test
Study – release it on the market
Act – Do analysis of the market. Discover which status product has in the consumer’s mind and which are the reasons for that.
Plan – Redesign product according to results given in the stage of analysis, PDSA
This is dynamic model which implies that end of one cycle follows beginning of the next one with intention of constant quality improvement where every cycle consist of all the steps. By using what we discovered in one PDSA cycle we can start a new, more complex one.
Realizing potential of PDSA and possibility of its application to every sphere of life (not only production process), Japanese managers transformed PDSA into PDCA methodology.
Why are those procedures and methodologies important for us?
In 1989:
- Internet, as we know it today did not exist.
- Mobile telephony did not exist.
- PCs were Commodore 64/128, Amiga and Atari (if you haven’t heard of them, everything is fine)
- Many of my colleagues and associates were not born.
- …
- Saga was founded.
Can you imagine how many business decisions needed to be make from then till now in order to keep company alive. Market has been changing since then. The way Saga and its clients operate changed beyond recognition. All those years Saga needed to develop, change, adapt to needs of clients and market. In the end company succeeded to enter forth decade of its existence and, even more important, to stay on top.
Most certainly, it was not easy to both follow trends and changes in the world of IT, and to continuously deliver high quality product/servise while operating in unstable environment.
Therefore, this jubilee is something to be proud of. However, all of us who are part of Saga this anniversary commits. We must continuously improve our business with new services, products and we must maintain at least same level of quality.
Described standards and methodologies, which are implemented in our business model, give us the right to expect to see Saga even more successful and recognizable at one of the next jubilees.
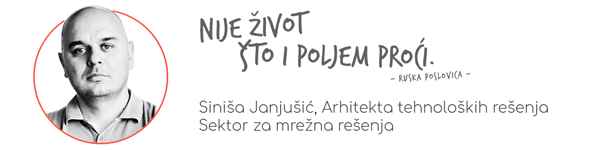